One-Month-Since-Kickoff Progress (There are so many parts to our robot!)
- ftc18094bbni
- Oct 17, 2021
- 5 min read
Can you believe it's been a whole moth since kickoff!? It felt like forever ago. So much has happened since then. Last week, we had completed the drivetrain, but we hadn't programmed it or tested it out (We were having a little bit of difficulties setting up the driver hub to do that). This week's progress has been a lot too. We got that driver hub working, managed to get the drivetrain rolling, and scrapped our entire idea for a claw on our robot and then redesigned it. Well, that last part probably wasn't super productive, but you get the idea. Oh and I almost forgot, we made amazing progress on a lift system for the claw. I guess our progress isn't 100%, but that's the way life is, right? Now, let me give you the details
First, drivetrain:
We finally finished building this week and we got it moving for the first time. It drives very smoothly and can even make it over the barriers that go on the field. This is our first major step in building the robot, and we are very excited to get the rest of it assembled in the near future. We have about a month before our first competition (check out our Events tab for more details) and we have a bunch to do to get our robot ready!
Second, claw:
Yep, we scrapped our entire idea for attaching the servos to the claw and make it move. Originally, we had our servos for each "finger" (if you'd even call it that) of the claw attached with a shaft and a hex-shaped bracket. When the shaft would turn in the servo, the claw would open and close. Our problem came up with the shaft adapter for the servo. Ours are made of plastic and last year, most likely because we were rookies and had no idea what we were doing, we stripped most of the little teeth off of the adapter and there was no longer a snug fit on the servo. This meant that the claw fell out of the servo even before we tried to move it. We had two solutions: purchase new adapters that aren't stripped or use one of the other servo parts we have. We decided on the second option (mostly because we are a little short on money to replace parts). We used a servo horn that could more easily screw into the servo, so that was more secure! And...I can't believe we didn't think of this before...the horn screws directly into the extrusion for the "finger" parts of the claw, so that was a little more secure anyways! It's a win-win there, and from what we can tell, this will work great for what we need. Initially we had a couple of concerns about the horn conflicting with the rubber band design we thought up before, but we were able to move a couple screws around to get it into place. Fingers crossed this works out when we test it out!
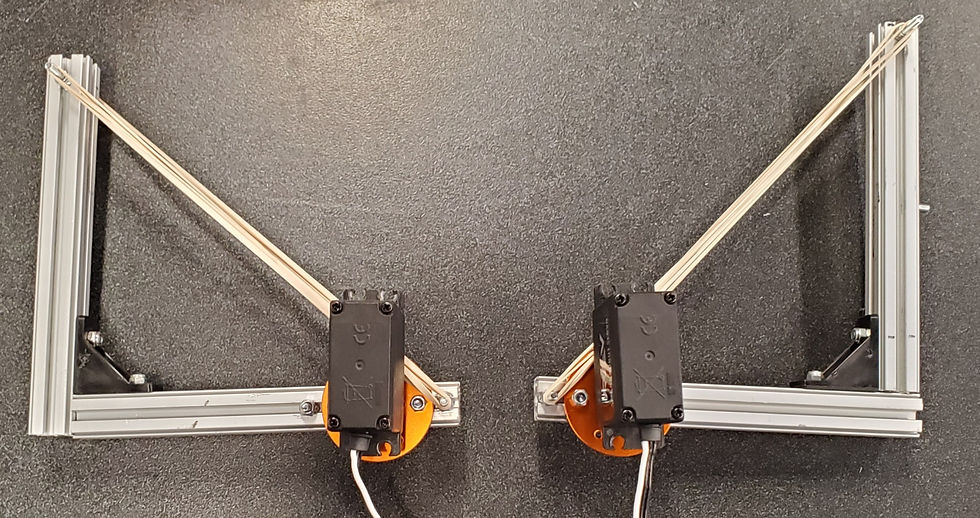
The setup for the claw (opened)
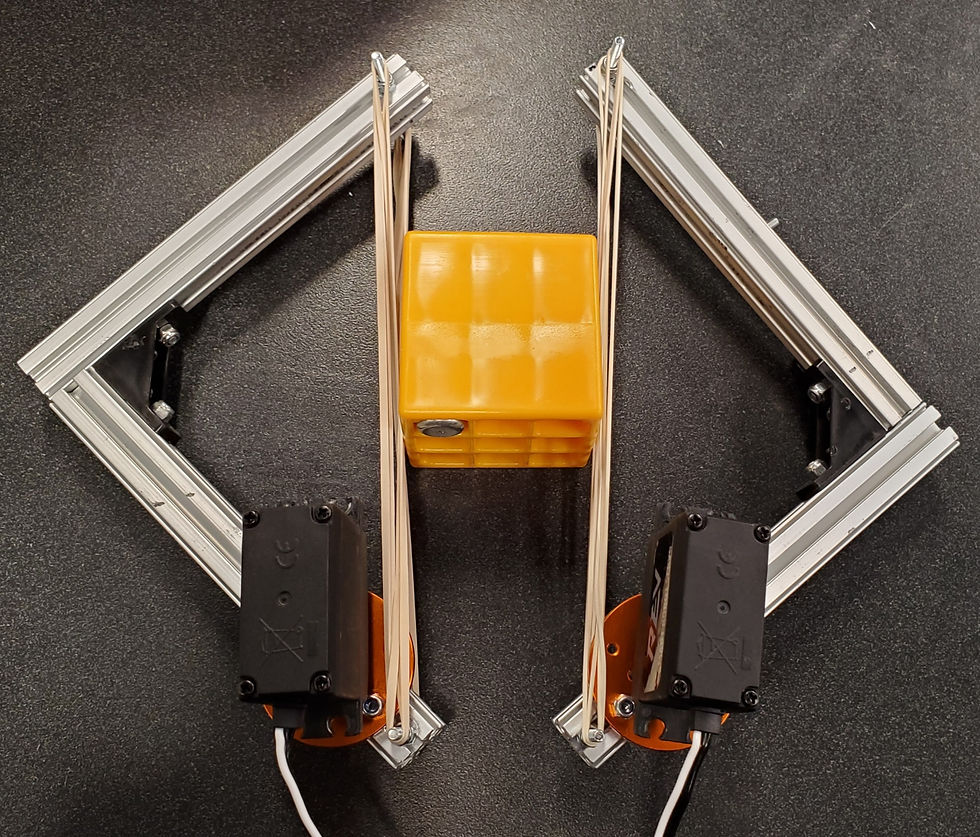
Grabbing a cube (There will be more pressure between the rubber band and the cube when we put it on the robot. This is just to get a rough idea of what it's going to look like)
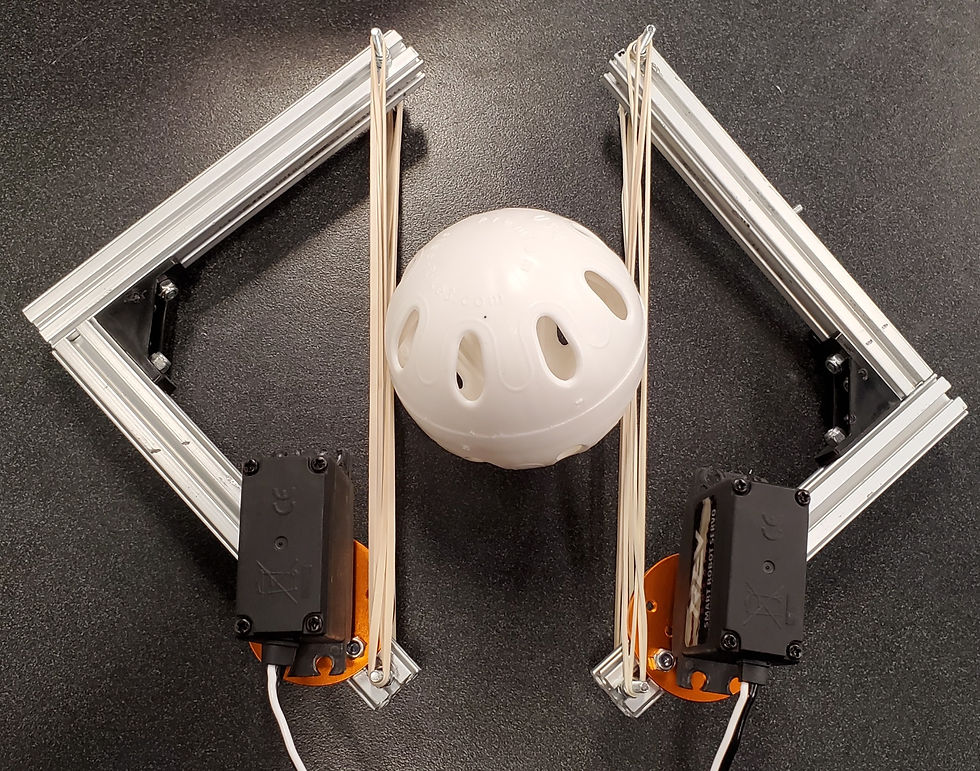
Grabbing a ball (Same thing with increased pressure when it's on the robot)
Third, the lift:
I know we haven't talked about this yet, but we've been doing a lot of work in the background. You know those lifting, elevator things that a bunch of teams used a couple years ago for the Skystone season? (I'll put a picture below if you don't know what I'm talking about) We plan on using something similar. It'll be cascading extrusions, operated by a pulley with our claw on the top so that we can lift the freight and our team piece onto the different levels of the shipping hub. We've got a kit partially assembled, but there are a few pieces we are missing and waiting to get right now. There's another big part to this lift: making it turn around. We didn't want to complicate everything with the drivers having to spin around and position the robot a certain way near the shipping hub because the field is so tight on space this year. We researched a little on how teams during the Skystone season did this (we didn't compete during that season). We found one team that created a giant gear underneath their lift system to be able to turn their claw around and set their giant bricks on top of the towers they were building that season. We decided that we could use the same idea for out lift. We are currently in the process of 3D printing our giant gear platform for our lift to attach to.
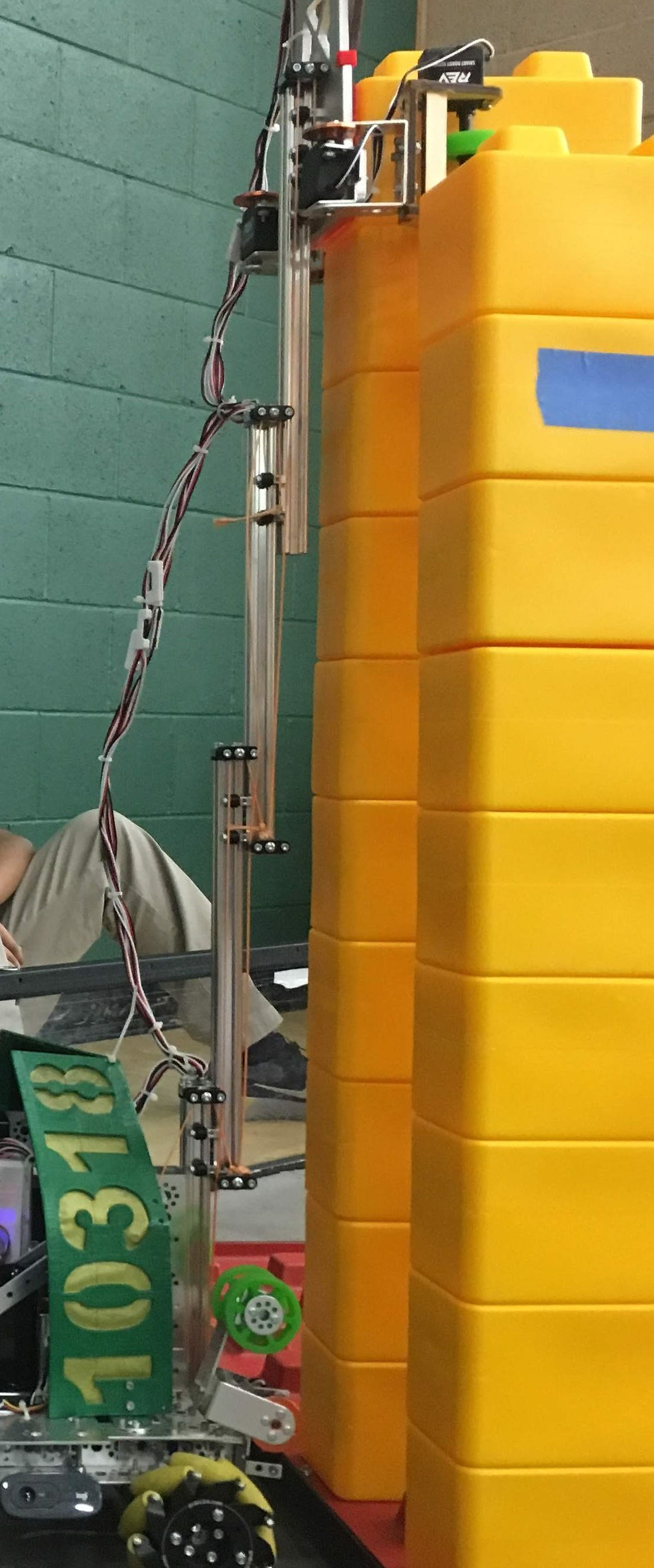
An example of the cascading lift from a Skystone robot
A compressed and expanded version of a section of our lift (not complete yet!)

A CAD of the rotating platform we are 3D printing
Fourth, the carousel spinner:
I didn't mention this at the beginning, but we basically finished this entire part, and there weren't too many design troubles that we found, so the story's not all that interesting, but it definitely makes for a much smoother build process when it's simpler. Basically all we did was attach a couple of those squishy wheels that a lot of teams used last year for flywheels to a shaft on a servo. There may be a couple of problems with the shaft adapter on the servo again, like we had with our claw, but I think we'll be able to rig the spinner so that it won't fall out of the servo.
A couple side notes:
We finished up our service project this week, and we've got our team game piece finished too! There's not a whole lot of interesting info around those, but I just thought I should mention it :)
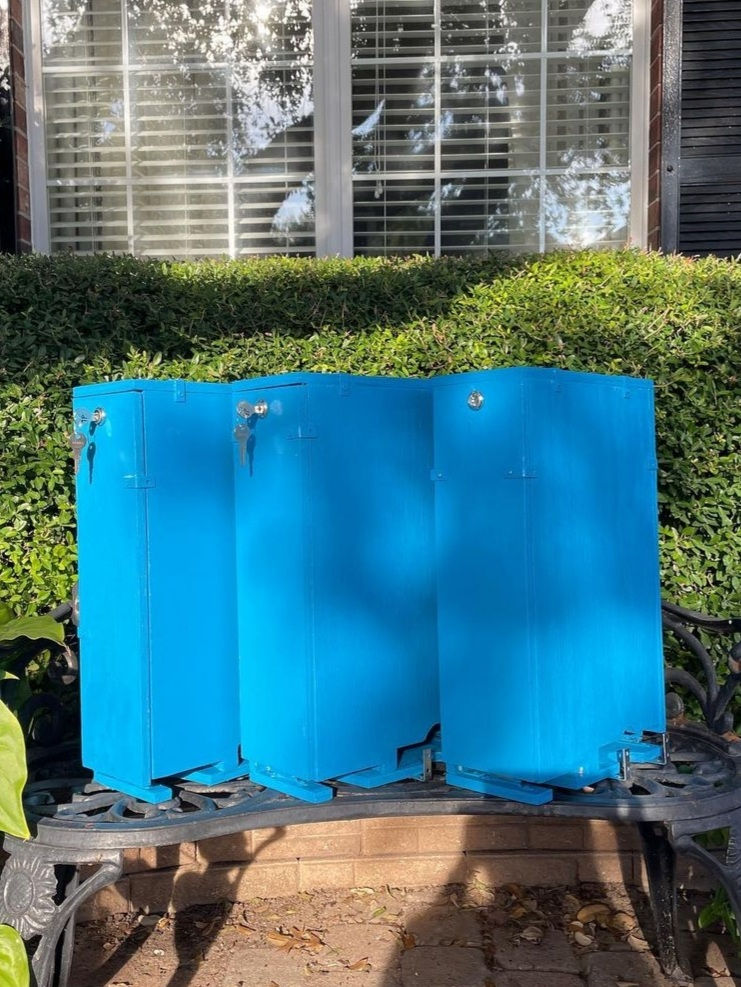
Finished dispensers (visit @optforactionbstx on Instagram or last week's blog post for the whole story)

Finished team game piece (I guess we now include one battery with this thing!)
I know this seems like information overload, and in some ways it is, but we want to be as transparent as possible with what's happening on our team and we want to be able to give you ideas when you get stuck like we get ideas from other teams on their websites and social media. Leave us a comment on this post if you like the content we're giving you guys or if you want to see something a little different in our blog posts.
Check out our surprise blog post from Tuesday. We are celebrated Walk like Woodie Day on Tuesday to honor Dr. Woodie Flowers and his legacy with FIRST, FTC, and other robotics competitions around the world.
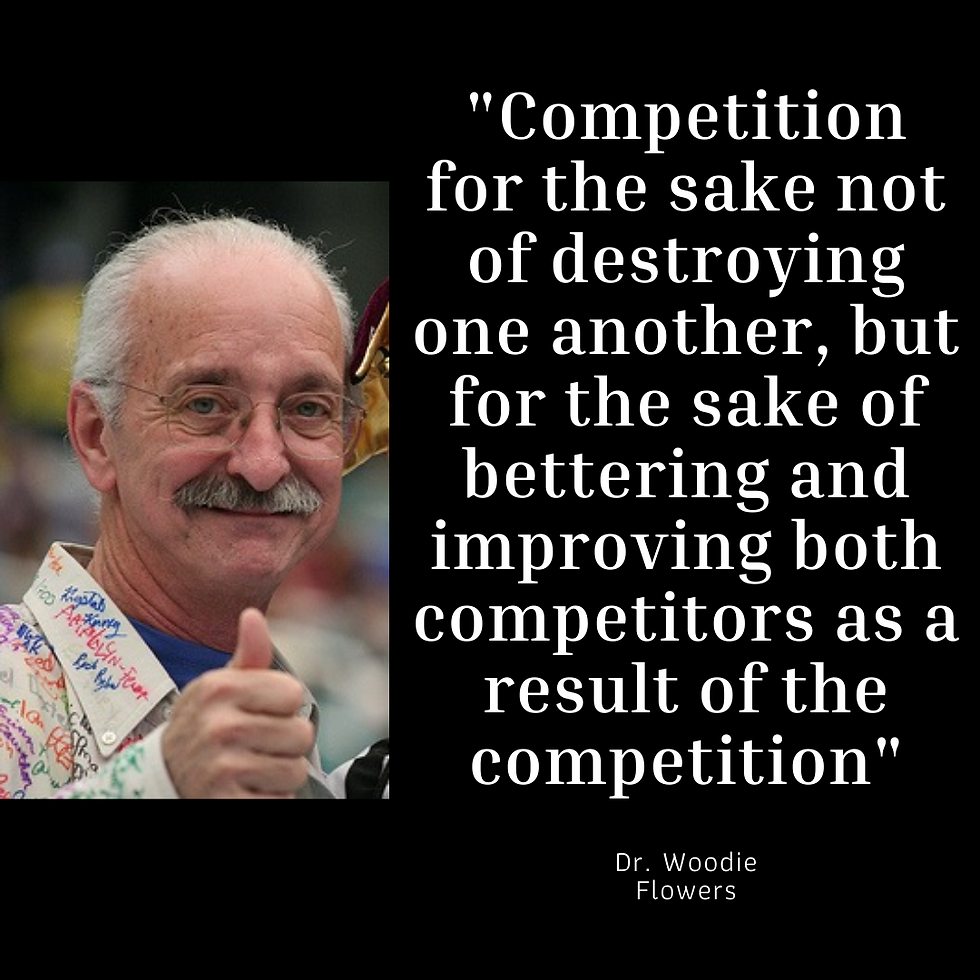
P.S. We got a few more Instagram mentions this week! This might get boring after a while. Thank you to @first_official_ for the mention in your story. And thank you to @REVrobotics for hosting the REV-o-ween Challenge this week and nominating our team as winner this week! (Give them some support and like over on Instagram!) We appreciate all the support everyone is giving us on Instagram. If you don't already follow us on Instagram, you should! (@batteriesnotincludedftc) We post more often on Instagram than on our blog, and there are exclusive pictures and content that you won't get anywhere else.
See you next week with another post! (We post on our blog every Sunday and on our Instagram throughout the week.)
Comments