Post-Match Redesign
- ftc18094bbni
- Nov 21, 2021
- 4 min read
I told you last week that there were a bunch of changes to make on our robot. Most of these ideas we got from other teams at our meet and are intended to help us improve before the next meet (which is in about 3 weeks).
First major change: the lift
Oh my goodness, the lift was sooooooo slow at the meet! We spent way too much time waiting for it to go up and down as we moved freight. It was completely inefficient compared to some of the other designs we saw (most of the faster ones had a lever-like arm that lifted the pieces up to the top of the shipping hub).
In the spirit of inspiration and helping each other out, we asked four or five teams at our meet about their designs, especially the teams that had a lever arm. There were only a few other teams that used lifts like us, but they used them at an angle so that they lifted freight up and out of their robot to set it on the top of the shipping hub. These were good designs too: very fast and efficient. But we had enough trouble to last us a season with our current lift, and we were tired of dealing with the lift not sliding well. We redesigned a mechanism like a lot of other teams used: the lever arm.
This arm will have a vertical fixed section on top of our rotating platform where our former lift was located. There will be another section, a bit longer, that can reach all the way down to the floor and hinge up to the top of the shipping hub. We have a pretty solid design for this and are pretty sure it'll work well. Many of the more experienced teams have used this idea and scored lots of points at the meet last week.

Our lever-arm design to lift the freight
Second major change: our claw
I hate to say it, but the claw is not going to work for this game. Don't get me wrong, it picked up pieces just fine and was able to score some freight onto the shipping hub, but it was too wobbly. About half the time we were carrying a piece of freight over the barriers in the warehouse, it fell out of the claw. It was probably something to do with the fact that the claw was so fragile and not very sturdy that it wobbled so much. The claw shifted a lot during the games we played and many of the freight pieces fell out of the claw as we moved around. The claw was great during our practice sessions before the meet, but with all the chaos of four robots on the field, it just got jostled around too much.
Our new design is to use a bucket with spinning wheels to put the freight pieces inside. We haven't fully hashed out all the details, but I'll explain the gist of the design. We'll have a plexiglass or acrylic bucket (a little more than 3 inches cubed) with two open sides and a trap door on another side. Intake wheels, not attached to the bucket, but to the bottom of the robot, will push the freight pieces into the bucket while the lever arm is at the bottom. The bucket will them be lifted up in an orientation so that the trapdoor side is on the bottom. The door will then be opened so that the freight falls down onto the shipping hub.

Our generic design for the bucket
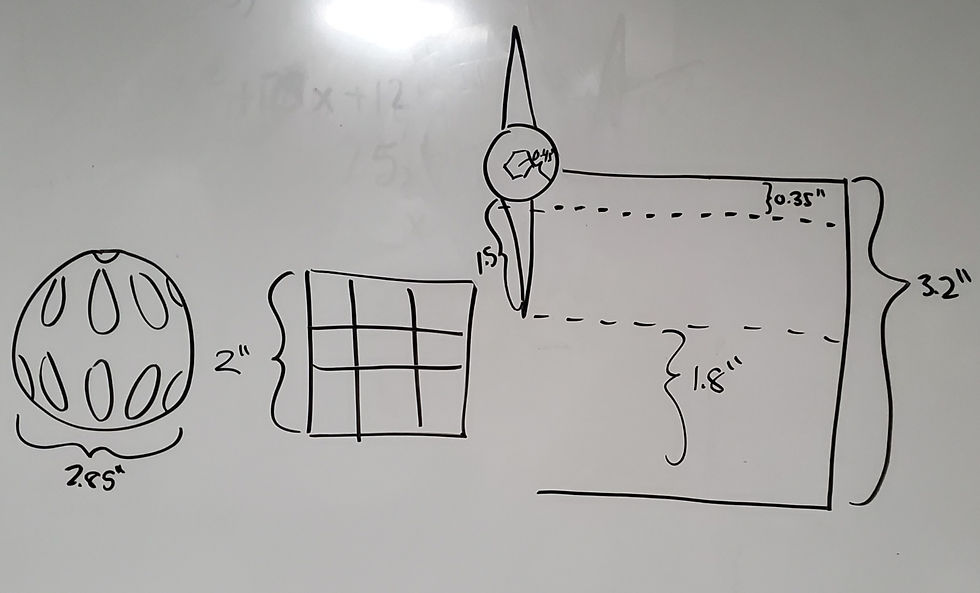
A few measurements and the intake for our bucket
Third (and final) major change: the wheels
We were quite the procrastinators before the meet last week, so we didn't get a whole lot of practice in before the meet. If we had, this problem may have been solved before now, but, you know, it just didn't play out that way.
The mecanum wheels we had on the robot slipped a lot on the barriers around the warehouse whenever we tried to go over them. They also caused us to bottom out on top of a block during one match! (That was supremely embarrassing.) The solution was extremely quick and easy to do: add grip wheels and omni-wheels. They both have a larger diameter and a more grippy surface that would go over the barriers better and without slipping. a quick change of wheels later, we were able to test the new design over a barrier. on the field.
It was so much better! The new wheels went over the barrier very cleanly. They were even able to go over when the robot was angled compared to the barrier (something we couldn't do with the mecanum wheels. We had to angle the robot perpendicular to the barriers to go over). They even allow the robot to clear the little triangle shapes that connect the barriers together. Those are a little taller than the rest of the barrier. I don't know why we didn't do this until now! The new wheels work amazingly!

Omni and grip wheels on the robot!
Right now, we are working diligently to take apart the lift and claw on our robot and finalizing a detailed design for our new systems. We are also waiting for some new parts to arrive in the mail before we can start diving into the building. Hopefully, these new ideas work better than our last. We hope to get started on building and finishing our robot this week and begin testing it out. We'll share the details and progress as it happens on our blog and on Instagram.
In the meantime....
Happy Thanksgiving everyone! We are so thankful for all the people and dedication that makes our team, league, and all the FIRST competitions around the world possible. Be sure to tell the people that mean the most in your life how grateful you are for them and to stuff away as much food as possible on Thursday!
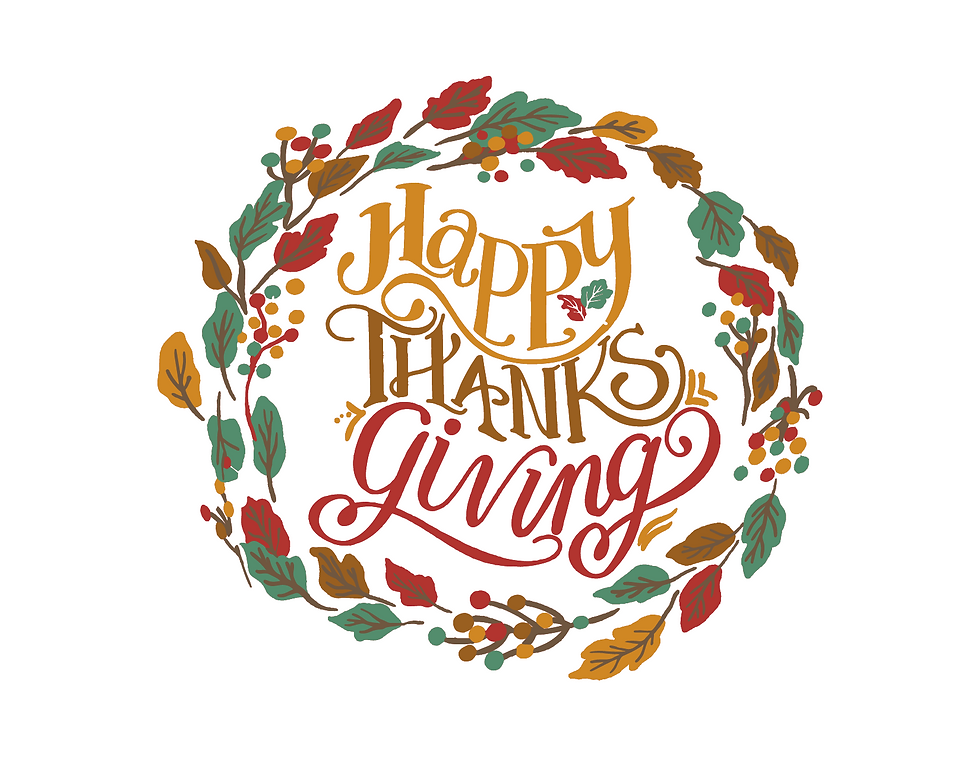
Comments